An open mixing mill (also called an open rubber mill) is a mechanical device used for rubber processing and plastic mixing. Its main function is to evenly mix, plasticize and modify rubber or plastic, and is often used in the production process of rubber products. The mixing mill consists of two counter-rotating rollers, and the material is processed by the shear force and friction of the rollers.
Principle of mixing mill:
When the mixing mill is working, the two rollers rotate relative to each other at different speeds. The materials accumulated on the rollers are sucked into the gaps of the rollers due to the friction on the roller surface, the adhesion effect and the adhesion between the materials. In the gaps, they are subjected to strong shearing and extrusion, causing deformation, which increases the interfaces between the components and forms a distributed mixture. This shearing will also bring great stress to the material. When the pressure exceeds the allowable stress of the material, the material will disperse and be wound on the high-temperature cylinder surface. In addition, due to the heat during shearing, the material gradually melts or softens. This process is repeated to achieve the expected melt-plasticization and mixing state to complete the plastic refining.
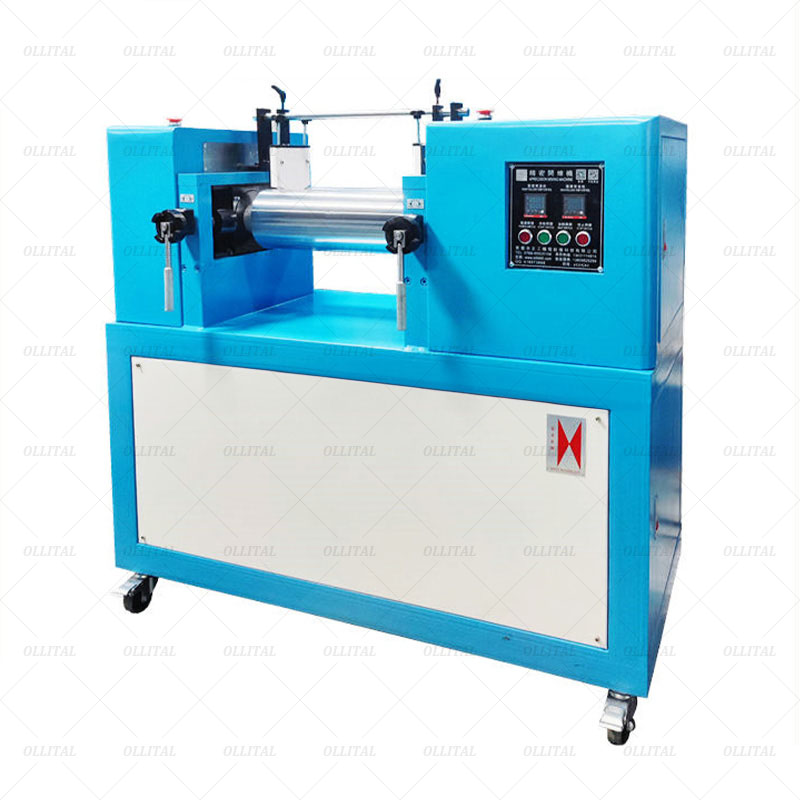
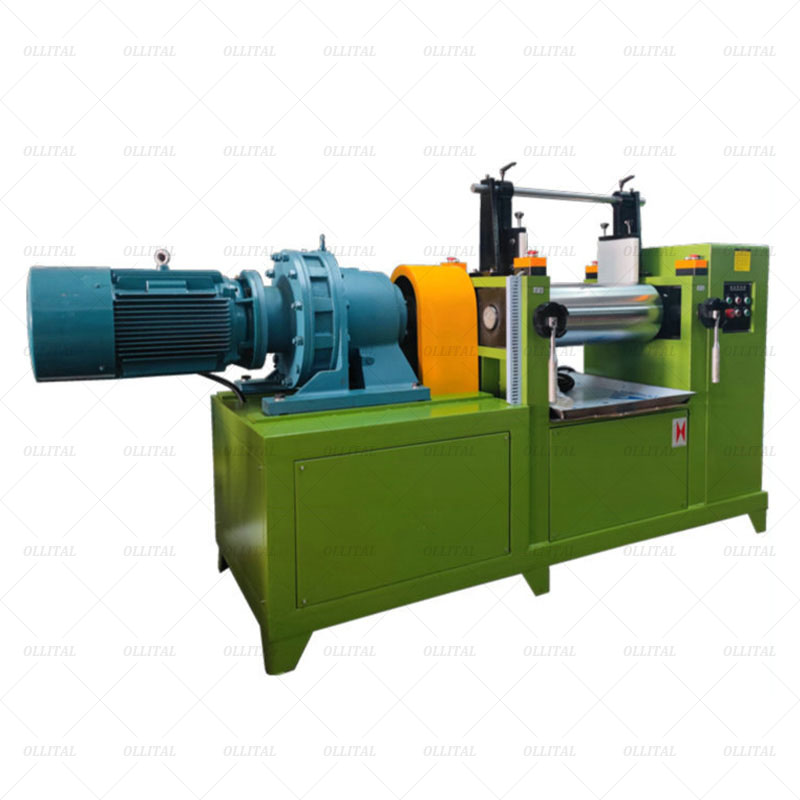
The main components of the mixing mill:
1. Roller: The core component of the mixing mill, usually made of steel, with a quenched surface for wear resistance. The two rollers rotate in opposite directions to process the material by shearing and extrusion.
2. Frame: Supports the entire equipment to ensure stable operation of the rollers.
3. Spacing device: Controls the spacing between the two rollers to adjust the thickness and shear force of the mixing.
4. Drive system: Usually an electric motor or other power system is used to drive the rollers to rotate.
5. Heating and cooling system: Ensure the plasticizing effect during the mixing process by adjusting the temperature of the rollers.
The main purpose of the mixing mill:
1. Rubber mixing: uniformly mix the raw material rubber with various additives (such as vulcanizers, additives, fillers, etc.).
2. Plastic mixing: refers to mixing various types of plastics and modifiers.
3. Material plasticization: using external forces such as heat and shear to change the rubber or plastic molecular chain to achieve the required processing conditions.
4. Calendering and pretreatment: pressing the material into a sheet of a certain thickness for subsequent processing.
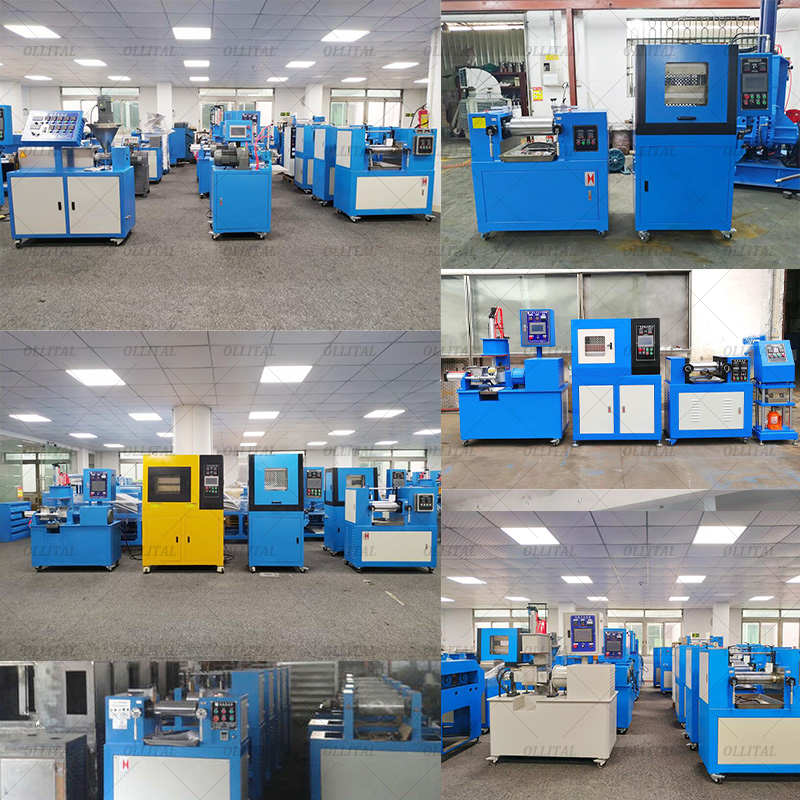
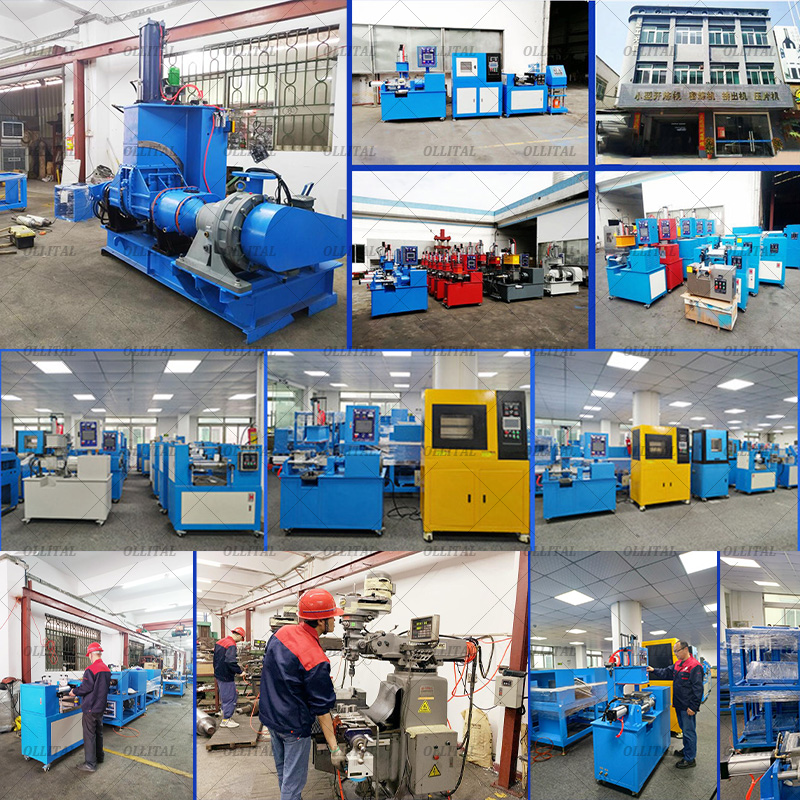
The mixing mill is easy to operate, highly efficient, and can adapt to a variety of formulas and material types. It not only has an important impact on improving the quality of rubber products, but also provides an efficient production solution for rubber and plastic manufacturers. With the continuous advancement of technology and the diversification of market demand, the design and function of the mixing mill are also continuously improved to meet more stringent production standards and a wider range of application scenarios.